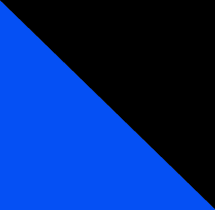
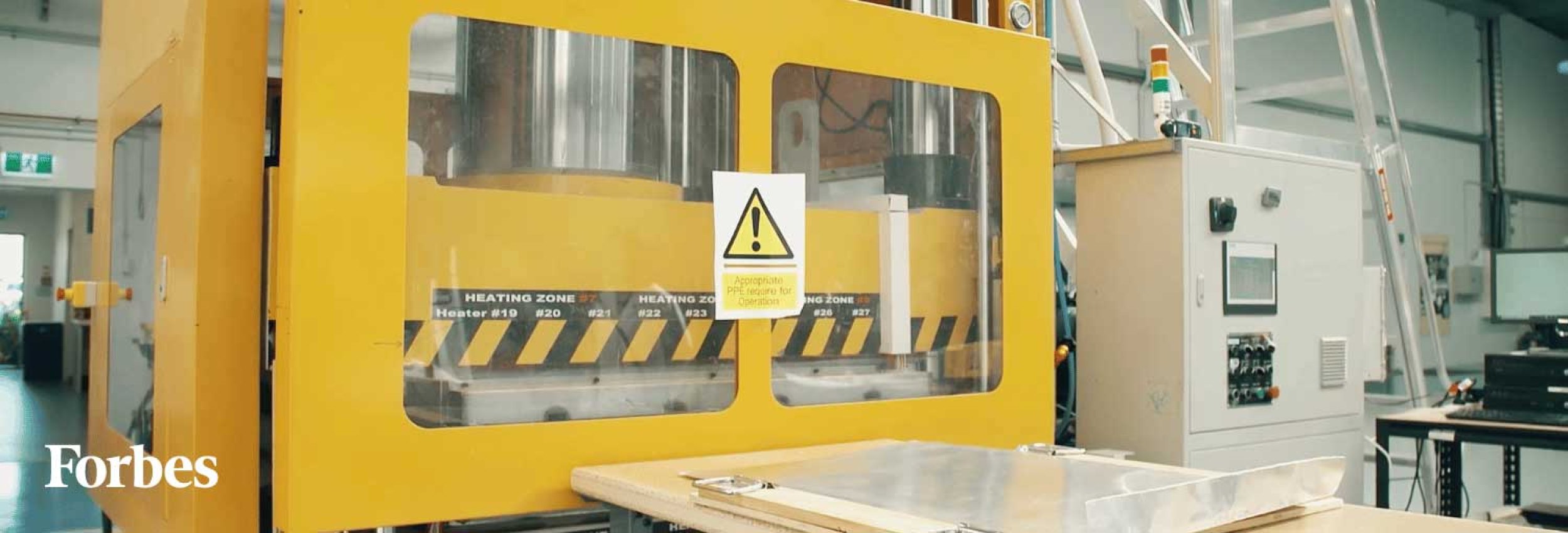
Forbes: Eliminating Microplastics And Cutting Emissions With Better Boards
2 May 2024
This article was originally published in Forbes by Erik Kobayashi-Solomon
The UN estimates that over a third of the 400 million metric tons of plastic produced annually is used for packaging, with only about 15% recycled. Much of this discarded plastic ends up in the ocean, breaking into microplastic particles entering the food chain. Plastic pollution is so severe the World Wildlife Fund predicts there will be more plastic than fish in the oceans by 2050.
New Zealand's NILO, established in 2018 by New Zealand entrepreneur, Tim Williams, is addressing this crisis. Led by CEO Glen Willoughby and advised by Sean Simpson, co-founder of LanzaTech, NILO has developed a technology that converts even normally non-recyclable plastics into a lower-carbon footprint alternative to traditional carcinogenic binders in particleboard manufacturing.
NILO believes it can use nearly two-thirds of the global waste plastic stream as feedstock for its industrial adhesive. What’s more, the production of NILO Binder has a carbon footprint 30% smaller than legacy products. Boosted by a 12.5% investment from IKEA last year, NILO is poised to make a significant impact on the plastic pollution crisis and on carbon emissions as its technology gains industry traction.
Company History
Founded in 2018 by New Zealand entrepreneur Tim Williams, NILO emerged from Williams' experiences in Japan, where he was the first foreigner to IPO two companies on the Japan Stock Exchange. Williams returned from Japan in 2010, determined to invest in local technologies that could promote the global good.
NILO’s first capital partner was Indigitech Ltd., a collective representing over fifty Māori whānau from various Hapū/Iwi. Glen Willoughby, a New Zealand executive with years of healthcare IT and bioinformatics experience, joined NILO in 2019 as CEO. Co-founder Sean Simpson, a native New Zealander who joined LanzaTech's board last year, also raised the company's profile. (See my articles about the amazing work LanzaTech is doing here, here, and here.)
Over the past few years, NILO has completed extensive development and testing cycles of its industrial binder, which is used to manufacture particle boards for ready-to-assemble furniture. This innovation caught IKEA’s eye, leading to the Swedish flat box powerhouse buying 12.5% of NILO’s equity in 2023.
Currently, NILO is building a pilot plant with a capacity of 10,000 tons per year, set to open in late 2025, with a plan to commercialize its technology by commissioning several 50,000 ton-per-year plants after that.
Technology
NILO's process innovates legacy wood fiber board manufacturing by replacing a toxic, carcinogenic, and high carbon footprint adhesive called urea formaldehyde (UF). NILO Binder generates fewer carbon dioxide emissions in its production process and emits no off-gasses, making the manufacturing process safer and more environmentally friendly while producing boards that are healthier to have in one’s home.
While I appreciate the lowered carbon footprint and human health benefits, I am even more interested in NILO's technology because of how its binder is made. The primary feedstock for NILO binder is plastic waste that would normally be incinerated or wind up making its way into the oceans and from there, into our food chain.
The company says it can convert nearly 60% of the 400 million tons of plastic annually produced—including normally non-recyclable varieties like marine plastics and films—into its binder. NILO Binder is combined with wood chips and compressed under heat to produce particle boards. Slight changes in the process allow for the manufacture of other wood products like MDF and plywood.
Willoughby told me that NILO is also testing the extension of its technology to develop a low-carbon cement substitute but is focusing now on the particle board industry due to regulatory changes discussed below. (For another company manufacturing low-carbon cement, see my article from November 2023.)
Climate and Ecological Impact
Using NILO Binder to replace UF has two significant environmental benefits:
First, it significantly reduces carbon emissions. The production of UF adhesives, totaling around 20 million tons annually, results in nearly 60 million tons of CO2 equivalents—comparable to the emissions from 13 million passenger cars yearly. NILO Binder, however, can be produced with about 30% lower carbon emissions, akin to removing approximately 4 million vehicles from the road. Additionally, using plastics that would otherwise be burned as feedstocks in the NILO process provides further carbon footprint benefits.
Second, NILO Binder contributes to a substantial reduction in plastic waste. Instead of ending up in landfills, being incinerated, or breaking down in the ocean, a significant percentage of plastic waste can be used as NILO feedstock.
Business
NILO enjoys a strong regulatory tailwind: recent EU rule changes, effective from 2026, will limit the use of urea formaldehyde in consumer products, and NILO’s facilities will be eligible to receive EU environmental credits related to reduced carbon emissions and plastics recycling.
The total available market size is also attractive. About 20 million tonnes of UF is produced annually in a market worth $16 billion.
NILO will generate revenue by licensing its technology to partners and by manufacturing and selling binder—which it will price competitively to UF. Its binder is engineered to be used as a drop-in replacement to UF, so existing particle board factories can use NILO Binder without retooling.
As NILO’s technology gains recognition, the company plans to license it to local partners and establish regional production facilities with a its standard facility producing 50,000 tons of binder annually. Currently, NILO is in discussions with three potential commercial partners, including IKEA.
With the tightening of EU regulations, Willoughby anticipates increased demand for NILO’s UF-free product. The capital cost for each NILO facility is relatively low at $23 million, with expected payback periods under five years from sales of the binder alone. Factoring in the value of environmental credits more than doubles NILO’s baseline returns.
Revenue from the wood fiber board business will be reinvested into R&D to jump start NILO’s commercialization of its low-carbon cement substitute.
Market and Competitors
EU regulations on formaldehyde are pushing companies to develop particle boards that reduce and eventually eliminate the use of UF. The Leadership in Energy and Environmental Design (LEED) also will not accredit products using UF adhesives.
Willoughby is confident that products manufactured with its binder will meet EU requirements and easily win LEED accreditation. Some companies, like Columbia Forest Products and Roseburg Forest Products, produce low-emission UF boards that may meet initial EU standards but would not win LEED accreditation. NILO thinks these companies reduce formaldehyde emissions by increasing the proportion of urea in the UF binder. This technique, NILO says, successfully drops formaldehyde emissions but also raises costs.
German chemical giant, BASF, markets a formaldehyde-free acrylic binder called Acrodur based on technology completely different from that which NILO uses. NILO’s engineers believe that if Acrodur was used in particle board manufacturing, curing times would be much slower, so again costs would be higher.
Research by Polish academics identifies substitutes like glyoxal and furfural as promising UF substitutes but notes technical challenges and high input costs.
There is so much plastic pollution in the world, it is hard to imagine that NILO would face competition for plastic waste feedstock. Some companies like Loop Industries and Agilyx use waste plastics in a chemical recycling process called pyrolysis, though. We should all hope to see a day where NILO, Loop, and Agilyx engage in bidding wars for plastic waste.
Eriks Take
On Earth Day this year, the Washington Post ran an opinion piece by Eve Schaub entitled Don’t waste your time recycling plastic. Schaub, the author of a recent book about plastic waste, makes the excellent point that…
“What passes for ‘recycling’ plastic is costly, energy-intensive and toxic. On top of all that, the process requires the addition of a shocking amount of new virgin plastic — around 70 percent — to hold the newly formed plastic item together. As a result, only about 5 percent of plastic gets ‘recycled’ (or, more accurately, ‘downcycled’ into a product of inferior quality).”
Schaub’s ultimate suggestion is to use a lot less plastic, which I agree is a sound idea.
That said, humans have already mined a shocking volume of hydrocarbons to manufacture an astronomical amount of plastics and will likely continue to do so for the rest of my life, at least. NILO’s team has figured out a way to bend the arc of an ecological tragedy into a circular economic solution that reduces the carbon footprint of a widely used product and improves human health. This is just the kind of thinking we need in this post-Climate world.
Intelligent investors take note.